The Cabinetmakers and Harpsichord Makers Play Favorites
Visitors to the Hay Cabinet Shop often ask us to name our favorite tool. On the face of it, this seems like an easy question; we do not need years of research to find an answer. However, it's a tough thing to choose a favorite among so many tools each with very different uses. Plus, will the unnamed tools feel neglected and stop working well? We are pretty sure the world does not work like that, but the relationship between maker and tool is such that we don’t necessarily want to take any chances.
While we think about which tool is our favorite at that moment, we drop a little snark to buy some time: “my favorite tool is a sharp tool.” Once the one visitor, among many, stops chuckling at that chestnut and everyone else stops rolling their eyes, we usually have an answer. There are five of us in the shop (three cabinetmakers and two harpsichord makers), and here is each of our favorite tool for the moment. As it turns out, the variety paints a nice picture of our two trades.
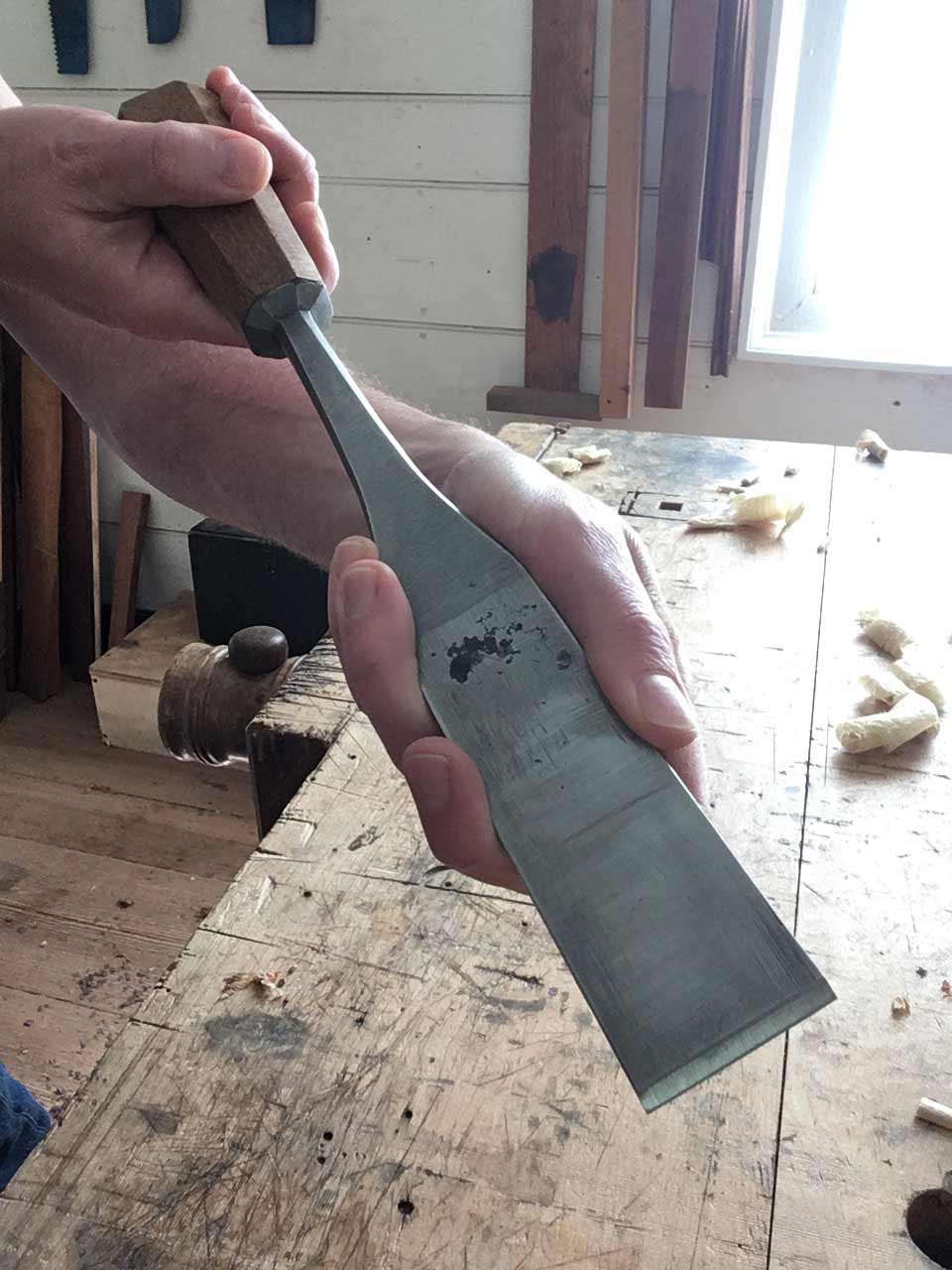
Bill Pavlak, Master Cabinetmaker
My 1-¾ inch paring chisel is one of my few tools in the Hay Shop that I wish I also had at home. This one was made by our blacksmiths and is just different enough from commercially available options and most antiques to make it special. Why do I like it so much? There are two closely related reasons: it is well balanced and comfortable to hold in a variety of positions, and it is a great multi-tasker. The chisel excels at accurately trimming joinery because of its great width. I can register the flat back of the tool against a reference surface and then use only a portion of the blade to make a controlled, guided cut (photo at left).
Part of the tool rides along what has already been cut while part does the cutting and so on. In contrast to that nitpicking accuracy, I also use the chisel extensively in sculptural work. As I shape the knees of cabriole legs, for example, I use this chisel to quickly hog of waste wood and then can make light paring cuts to clean things up (photo at right). In this case, it’s the tool’s great length that allows my hands to generate a lot of power. While that versatility is wonderful, I also love this tool because I know the people who made it – that makes it all the more special.
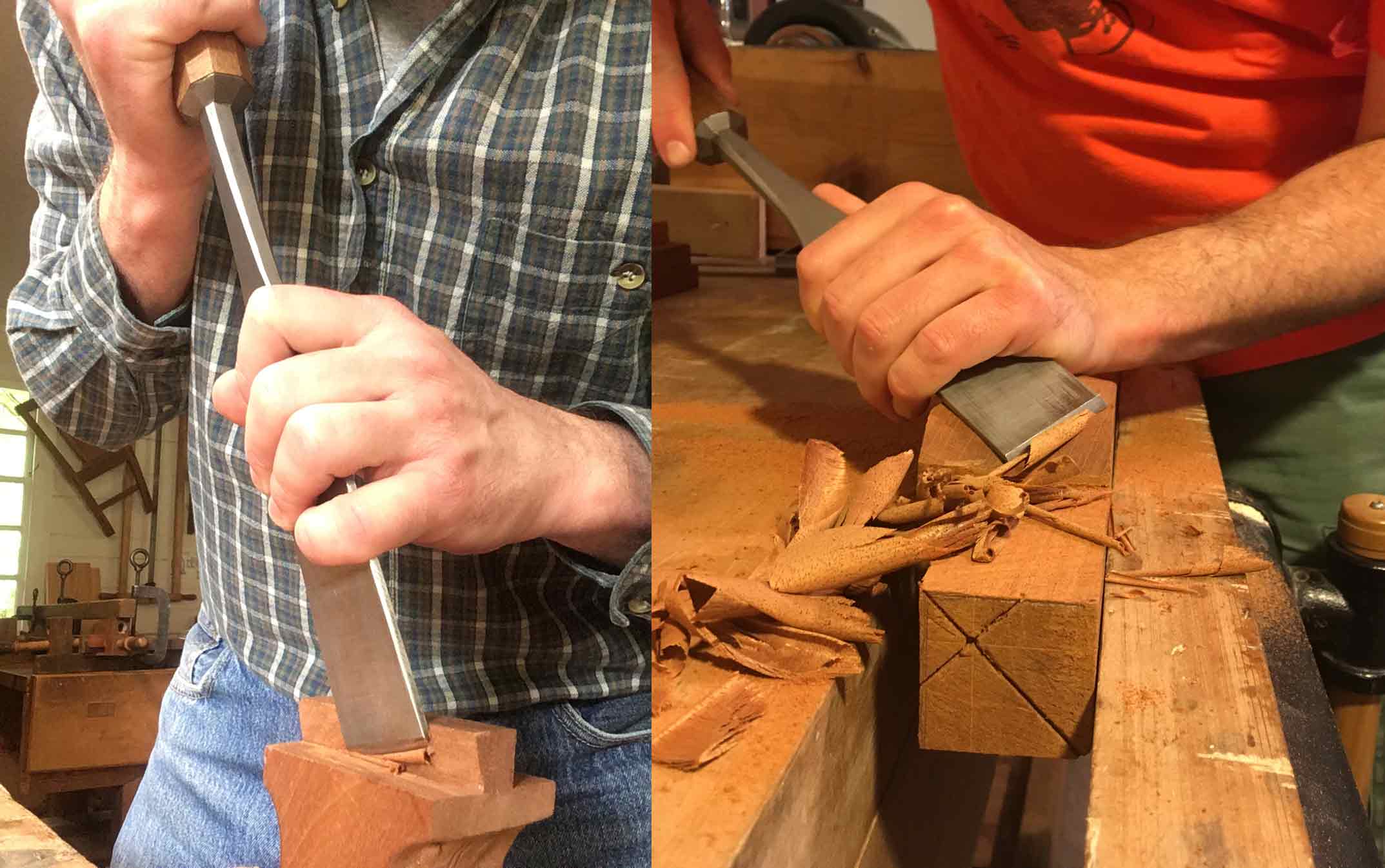
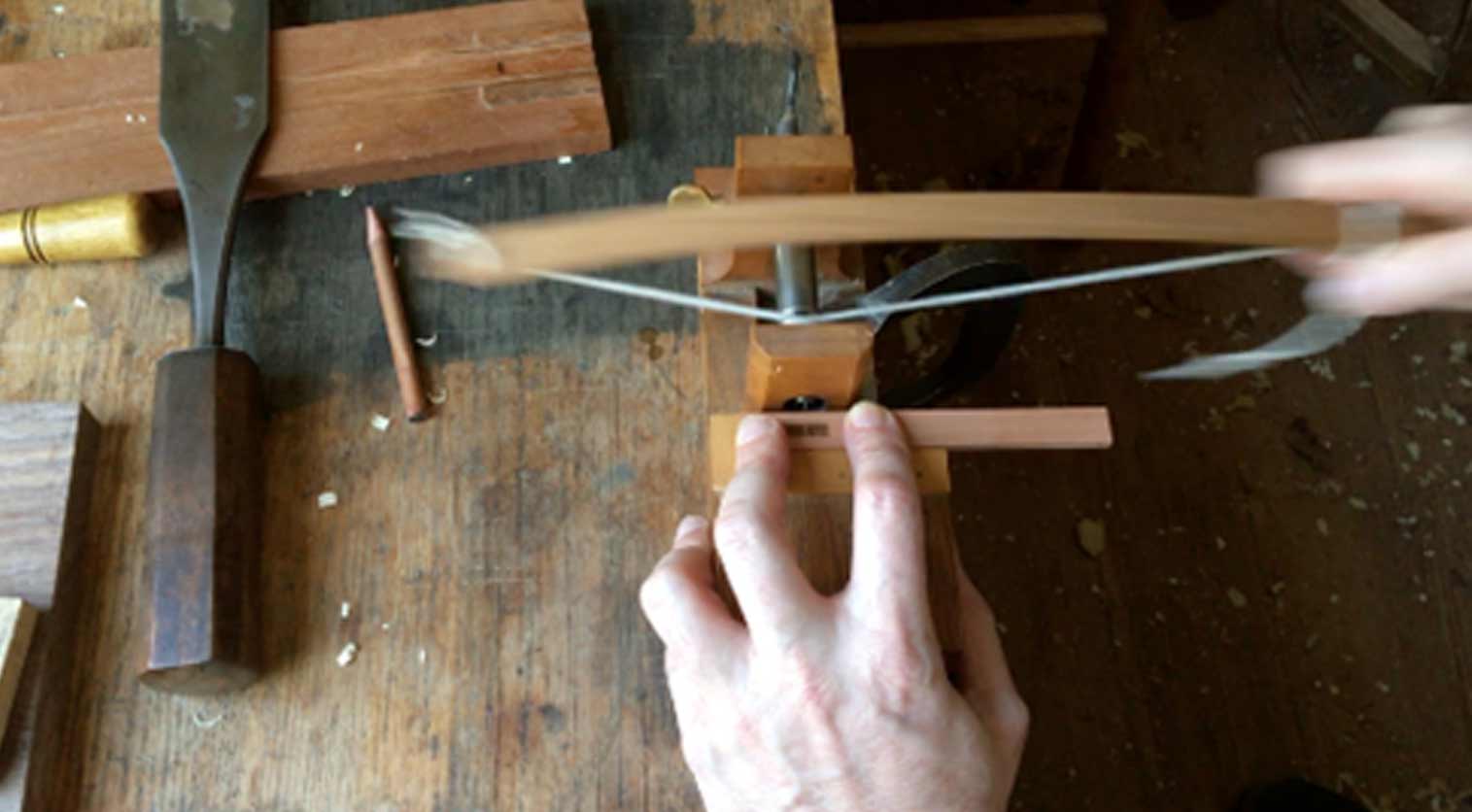
Edward Wright, Journeyman Harpsichord Maker
My favorite tool is a small drill press operated by a bow that I use for boring the tiny pivot holes for harpsichord jacks (the mechanism that plucks the instrument’s strings). Based on a design from J. A. Roubo’s woodworking treatise of 1769, the tool makes for controlled, lateral work, with the drill supported in the stock and the jack body and tongue held to a small carriage. A dressmaker’s pin makes the bit. With the bowstring wrapped around the body, the worker rotates the drill back and forth while at the same time guiding the jack as the bit cuts. With practice and finesse, it makes short work of drilling dozens of jacks needed for the complete action of a harpsichord.
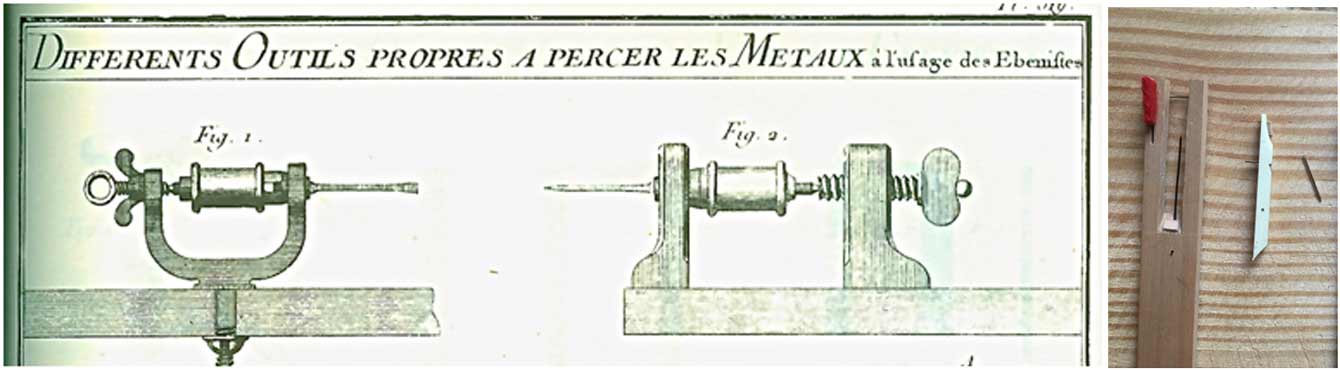
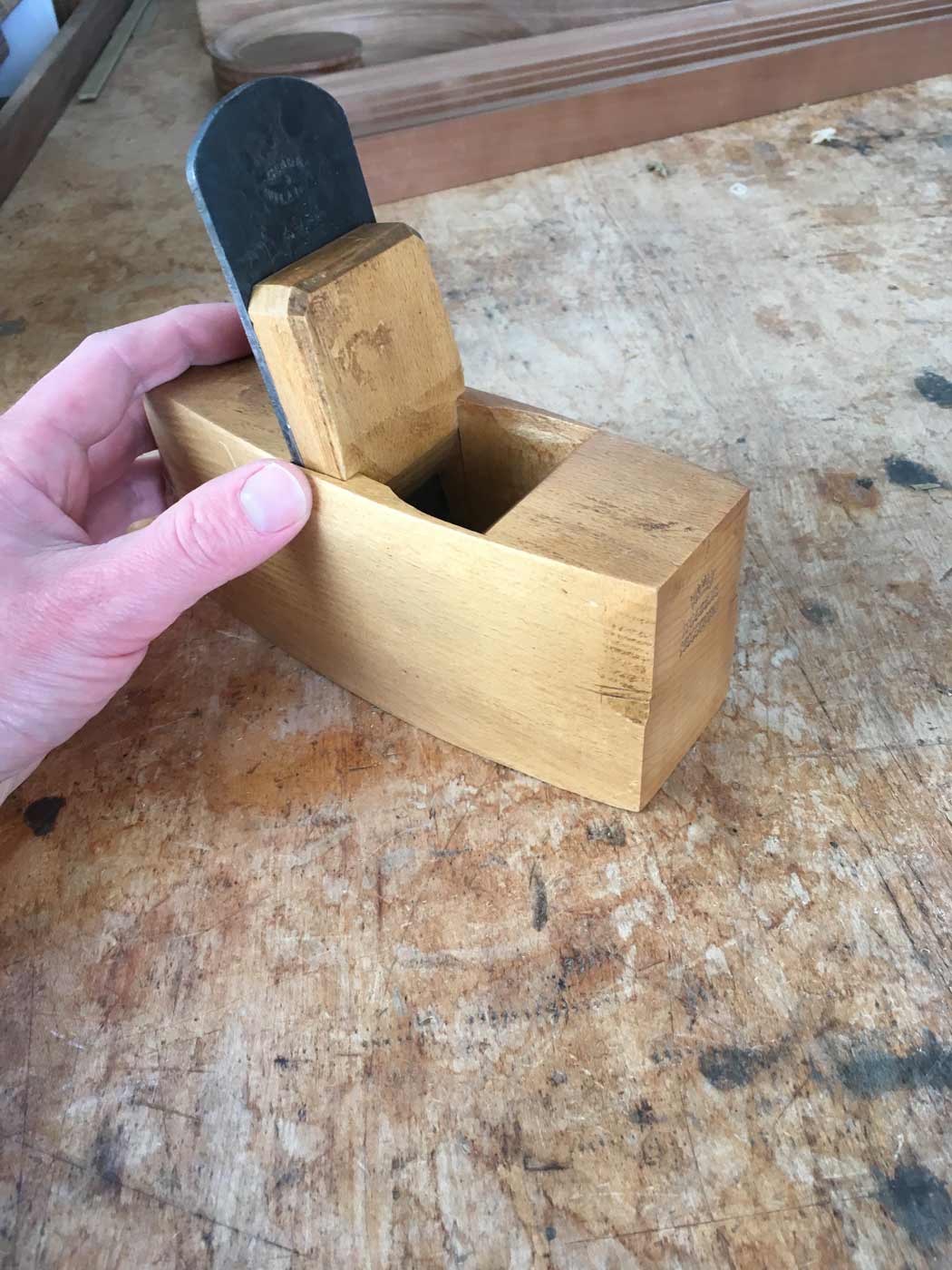
John Peeler, Apprentice Cabinetmaker
One of my favorite tools in the shop is the toothing plane. At first glance, it appears similar to a regular smoothing plane, which shaves wood curls away to leave a smooth surface, but the toothing plane works very differently. It has a blade with tiny teeth at the end of the cutter instead of a straight knife edge. That blade is also at a much higher angle to the bottom of the tool than normal planes. There are many uses for this plane in a cabinetmaking shop, but I use it most often for planing woods that have very difficult, beautiful grain patterns like the tabletop pictured below. These tricky woods don't like to be smoothed with normal planes, which will tear out the fibers of switching wood grain. The toothing plane, because of its high angle and serrated cutting edge, isn't bothered by grain direction changes. I can use it to remove wood from a board without fear of a ruined job. The only downside is that the surface left behind has a coarse, rough feel. To fix this, we can use tools like scrapers for the final smoothing, but the toothing plane is what I reach for first.
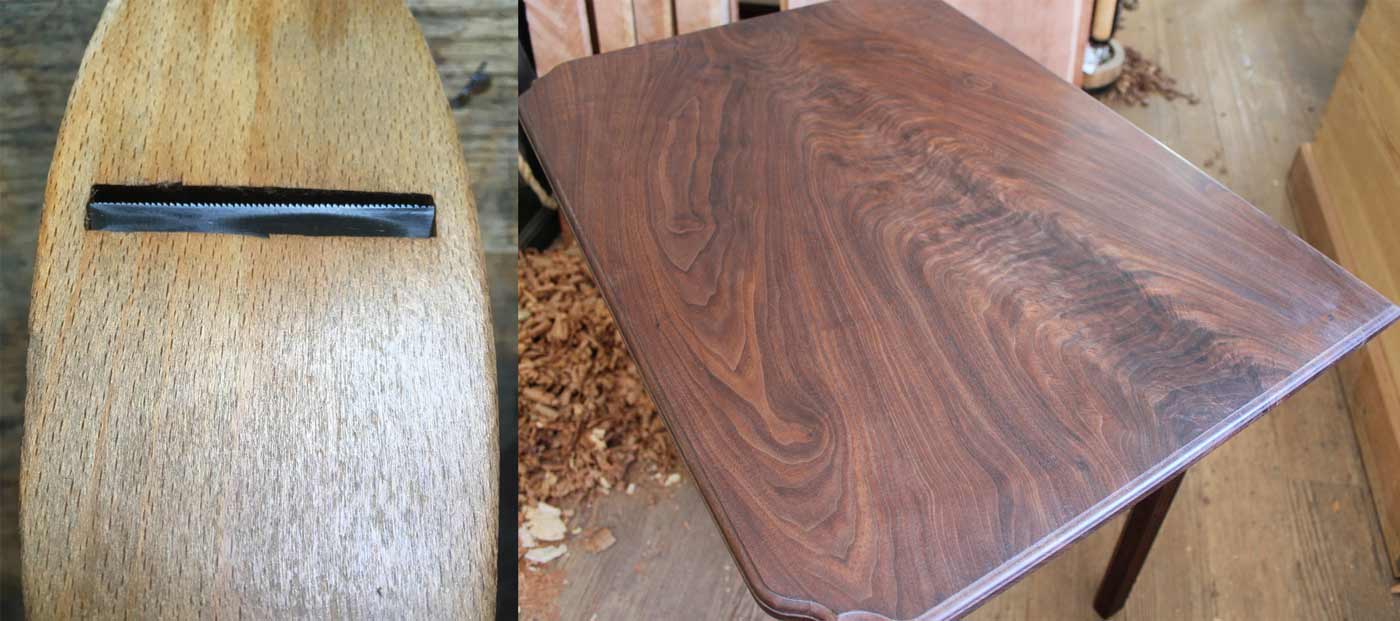
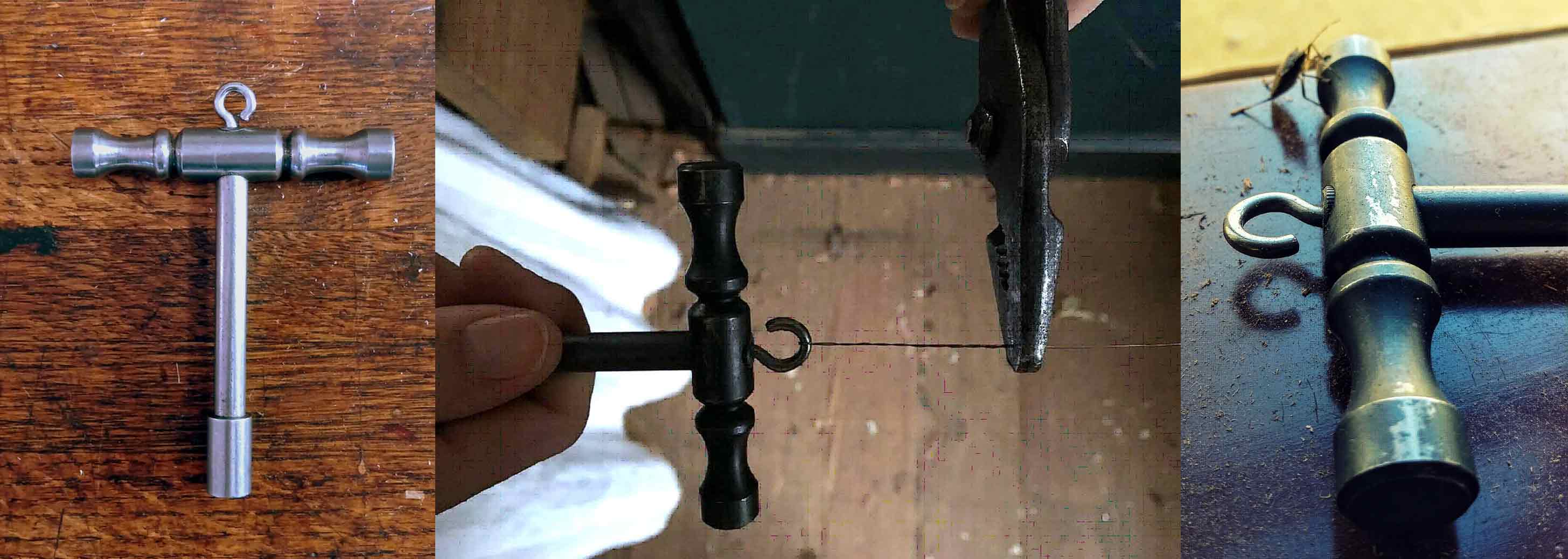
Melanie Belongia, Apprentice Harpsichord Maker
The tuning hammer is one of my favorite tools in the shop. It is a versatile little multi-tool. Tuning pins on historic keyboard instruments weren’t standardized so most of the time a tuning hammer was included with the instrument for tuning and maintenance.
With the hammered ends, I can strike the tuning pin to lock it into place in the wrestplank during string replacement. The socket on the end of the stem is for tuning. By putting the socket over the tapered head of a tuning pin, one can turn the hammer clockwise and raise the pitch of the string, making it sharper, or turning it anti-clockwise, thus lowering the pitch, making it flatter. The hook on the end (sometimes removable, and therefore lost to time, on historic tuning hammers) allows me to wrap the loop on the end of a string when installing/replacing string wire. And the hook keeps me from misplacing the hammer; it tends to live on my apron while I'm in the shop.
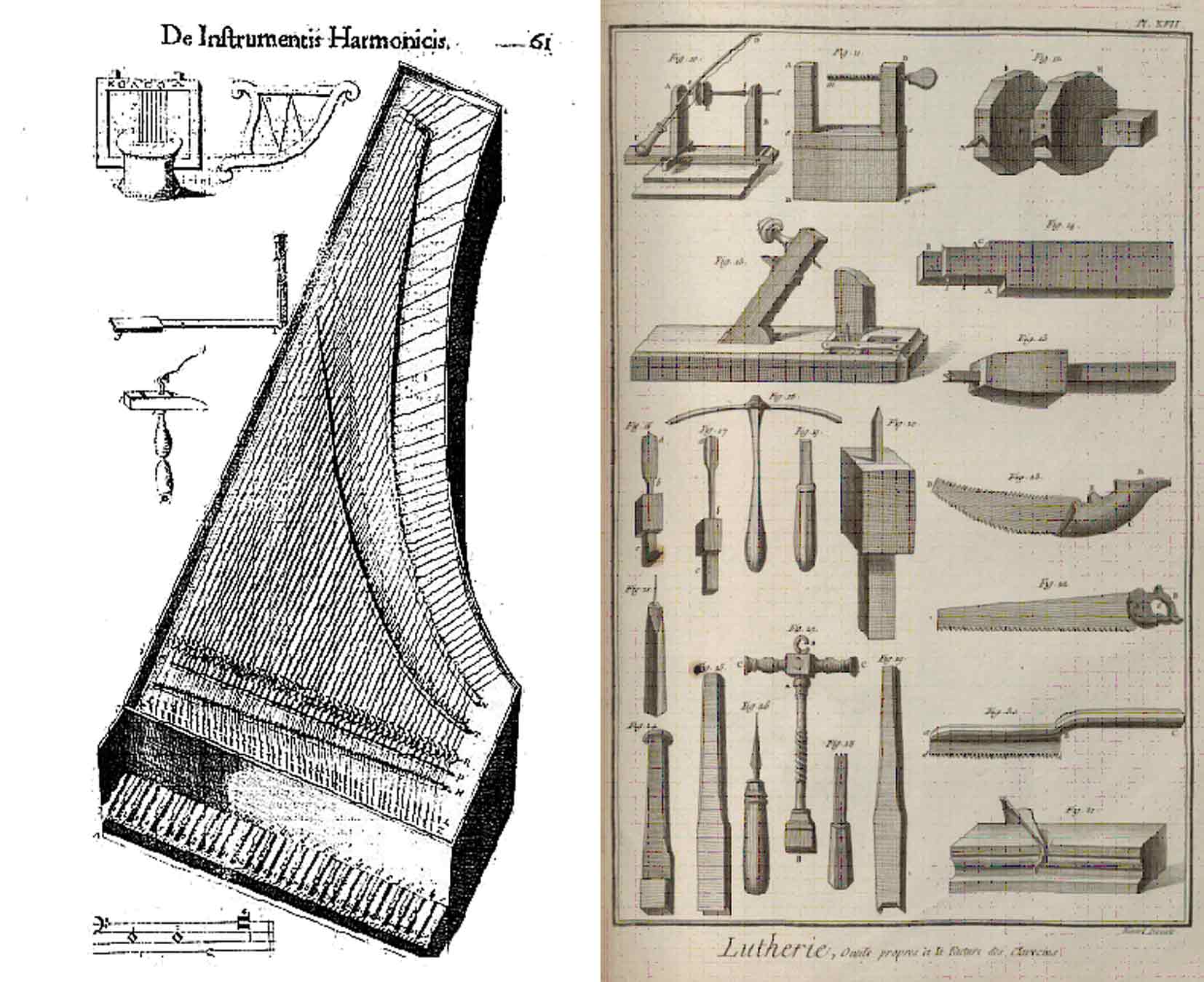
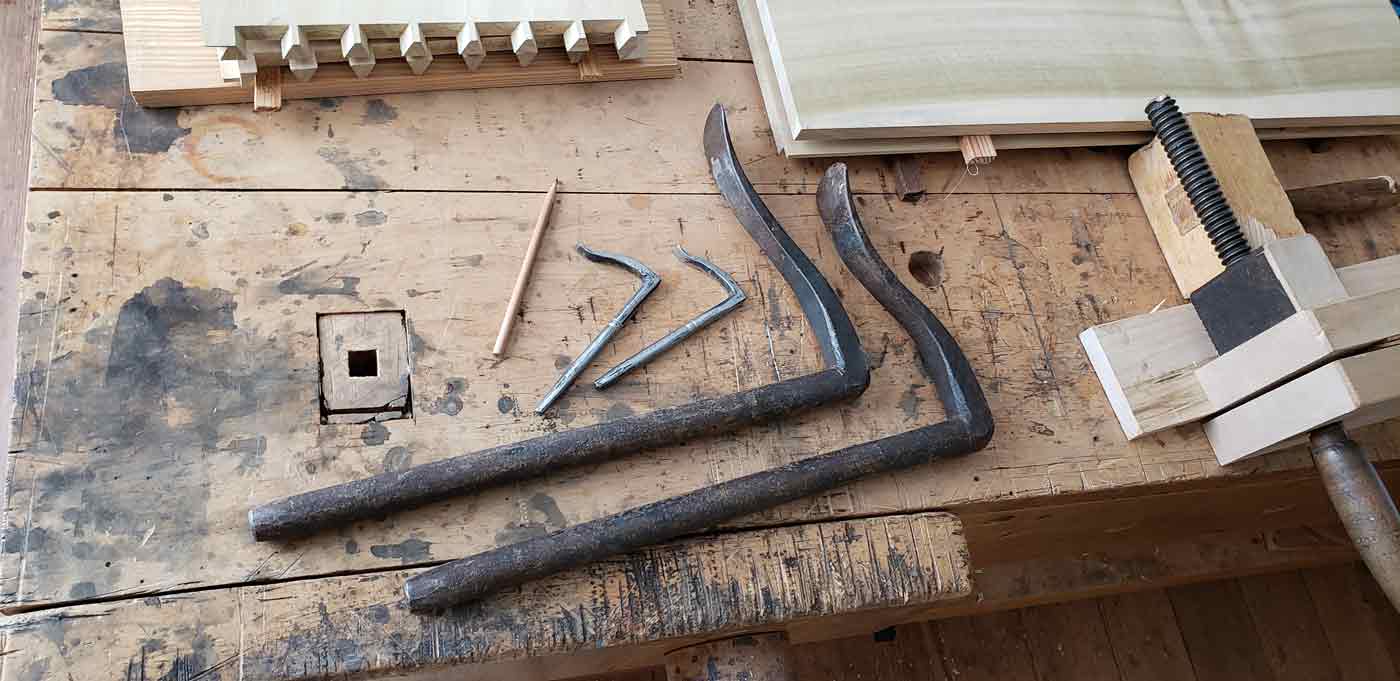
Jeremy Tritchler, Apprentice Cabinetmaker
Holding work securely to a bench is one of the most important and challenging parts of woodworking, so something I find myself reaching for repeatedly on almost every project is a very simple tool for clamping work to the bench: a holdfast. The holdfast is a single piece of bent iron bar stock with a flattened pad on the end. It is used to clamp workpieces against the surface or side of a workbench. Many workbenches have several holes drilled into their top and sides. These holes are just a little bigger than the diameter of the long shaft of a holdfast. To hold a board down, the holdfast is slid into one of these holes with the pad resting on the workpiece. The holdfast is then tightened down by hitting the top of the shaft with a mallet, causing the shaft to angle and wedge itself in the hole while also pinching down on the board. Holdfasts can hold boards of all shapes and sizes in a variety of different positions, making them like an extra set of hands while working, and hands are something I always find myself short on.
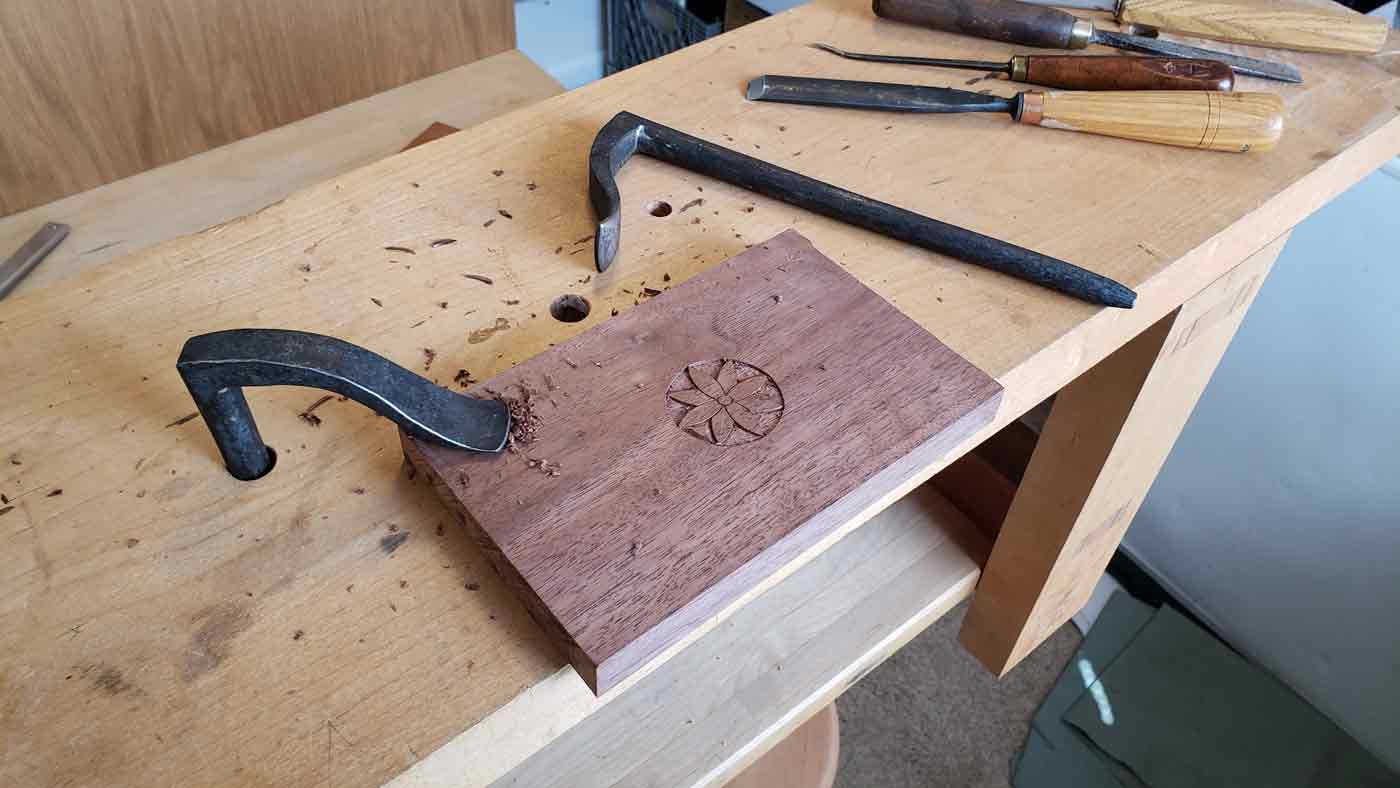